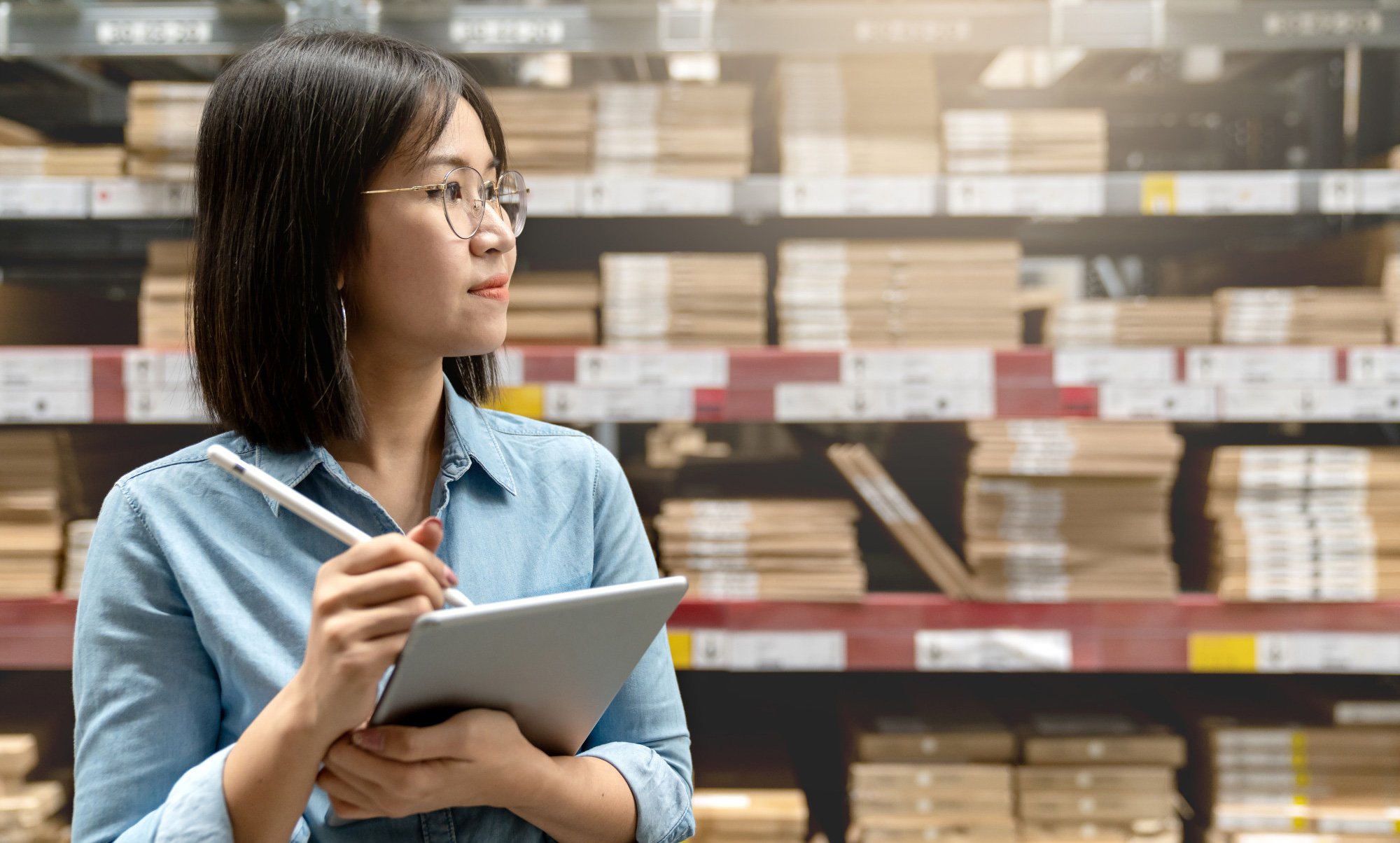
At the beginning of the pandemic in March 2020, the World Health Organization pushed for hospital manufacturers to increase the production of personal protective equipment by 40%. Two years later, the world is still struggling with sluggish supply chains, a lack of employees, and poor communication.
You may have considered how to improve your warehouse management and combat some of the problems of inefficient supply chains. We have a few solutions for you that you don't want to miss out on.
In our complete guide, we go over our top three tips to improve your warehouse management through technology, organization, and proper training. Keep reading on and learn more!
Tip 1. Proper Organization
A poor organization can make you feel that your hospital warehouse management lacks adequate space when ordering and receiving shipments. In reality, the likely cause is a lack of organization. Instead, take the time to itemize and organize your warehouse through a warehouse management system.
To start managing hospital warehouses, you need bins, carts, racks, and inventory scanners. Finding durable and space-friendly equipment can improve haphazard organization. In return, it should enhance the efficiency of checking items in or out.
Lastly, organizations cannot be changed solely with technology. You need your entire team on board, including current vendors and contracts. With supply chain difficulties, you can improve your organization with vendors and manufacturers by:
- Hiring a supply chain consultant
- Renegotiating old contracts
- Locating new contracts
Teaming up with local suppliers can reduce the stress and risk of relying on overseas shipments. Supply chain consultants can be useful in these situations if you are treading in unfamiliar territory.
Their main role is to help you maximize supply chain productivity and efficiency. Consultants also educate regarding best practices and methodologies.
Tip 2. Smart Inventory Tracking
Smart inventory tracking uses technology to help order, receive, and stock your hospital warehouse. Coupled with analytics and you can determine when you need to place resupply orders.
Hospital supply chains are convoluted, and many hospitals continue to face shortages. For example, a year ago, N95 masks were being distributed from nationwide factories by the millions. Yet, thousands of hospitals remained undersupplied from poor communication between manufacturers, federal regulations, and hospital management.
Even when barriers such as N95 mask shortages arise, smart inventory tracking gives you detailed stock-out or surplus reports. Other benefits of BlueQ Analytics compared to traditional ERP solutions are:
- Spend reports
- Hospital warehouse management report
- PAR management reports
- Labor/time management
- Data-bin sizing metrics
- Optimization reports
Ultimately, it gives your management team oversight of the entire hospital supply chain. It includes details from the initial steps in the manufacturing process down to the shipment. With better insight, you can develop better emergency plans.
Tip 3. Rotating Bins
Many warehouse management hospitals struggle with medical waste. This comes in the form of unused or expired items. Primarily, medical waste arises from a lack of proper stock rotation.
When new items arrive at the warehouse, they are placed in front of older supplies, increasing the chances of expiration. Not only does this lead to problem number one (lack of adequate warehouse space), but it slows your system and creates more disorganization.
Many medical supplies have short expiration dates, such as insulin. Unopened insulin can be stored until the listed date if placed in a refrigerator. Unopened vials outside of a refrigerator will expire after 28 days.
Without adequate rotating bins, you have higher risks of critical medications and supplies that will be unsafe for human use. The 2-Bin Kanban Inventory Management System is an excellent solution for managing your stock.
It is easy to manage and scalable for your business. BlueBin Kanban Systems help you standardize your inventory system by:
- Using visual replenishment guides
- Ensuring supply delivery to the right place
- Improving space requirements
- Rotating stock
Ultimately, it can save you a significant amount of money and time. Research shows that the BlueBin Kanban system helped hospitals improve supply chain efficiency by 30%. It also reduces supply holding space by 25%.
Will Hospital Supply Chains Improve?
The past two years have pushed warehouse management teams to think of new and creative ways to stock critical supplies. Most are wondering if and when the system will improve.
While unfulfilled promises in supply chain struggles have negatively impacted warehouses, experts found something more critical. They discovered that inaccurate inventory records are one of the primary pieces that:
- Increases costs
- Delays stock demand
- Reduces revenue
The international supply chain may take months before it reaches pre-pandemic levels. Initially, experts predicted a return to normal by 2023. That has since been pushed back from the recent war in Ukraine.
During this time, it is crucial that other components are fixed. Inaccurate counting policies and lack of accountability can contribute to shortages.
Regarding inaccurate counting policies, you need a system that tracks and notifies you of low or surplus stock. Manually stocking and counting items can set you up for errors that later contribute to out-of-stock supplies.
Second, lack of accountability is fixed by hiring warehouse managers. You need employees with clearly defined roles working with and managing your warehouse inventory for the best results.
Warehouse Management Strategies
Your warehouse management relies on efficient inventory tracking systems to keep your facility up and running. Without trained staff or the use of advanced technology, you could suffer shortages or loss of revenue.
BlueBin is here to help hospital warehouse and inventory systems such as yours. We have developed a BlueQ SmartScan system that gives you handheld access to your entire supply chain process.
Are you ready to get started? Check out our BlueQ Smartscan device and discover how it can revolutionize your warehouse management.