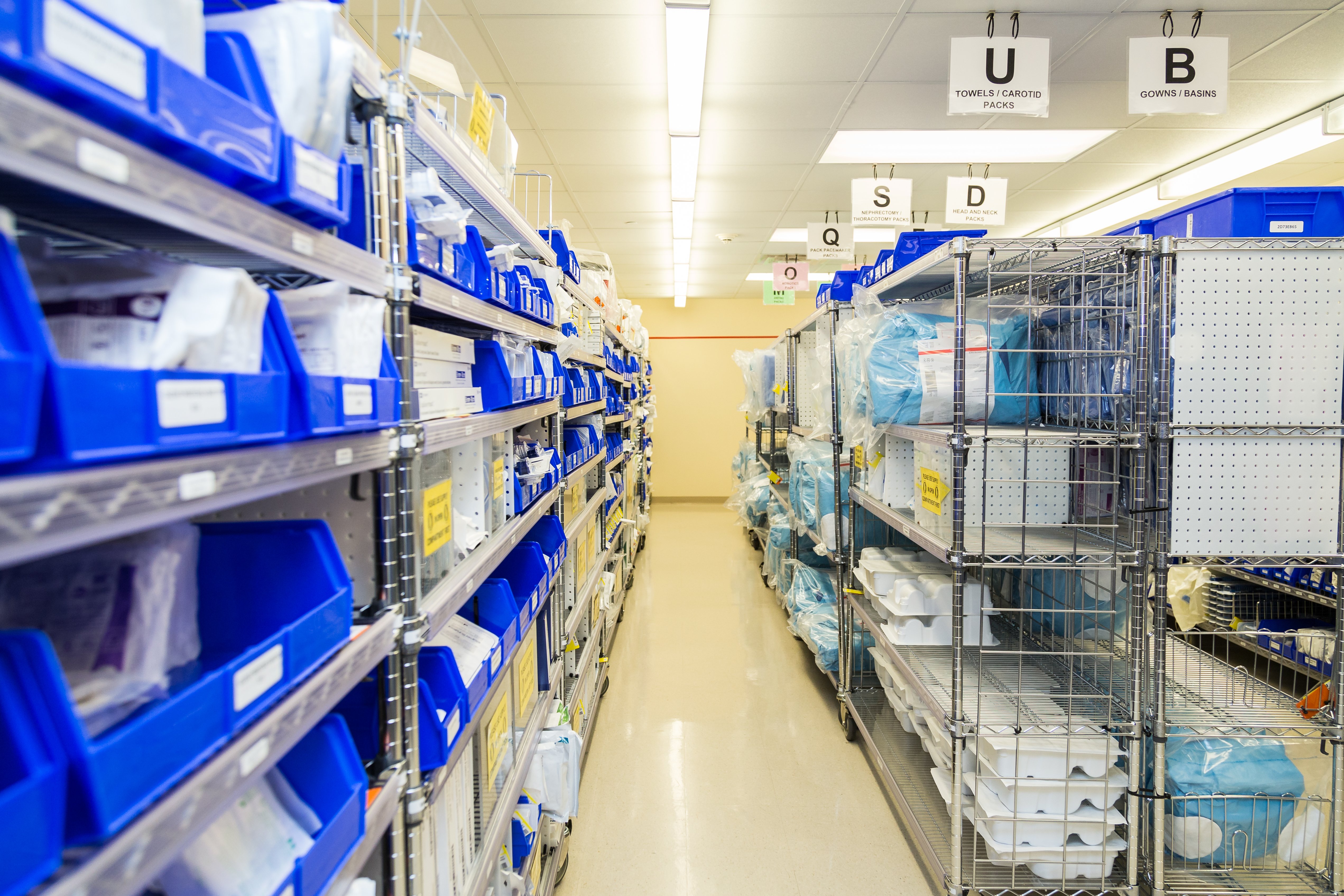
As many people are well aware, the COVID-19 pandemic has magnified healthcare industry supply inventory issues. A February 2021 survey of 100 nurse leaders reported key consequences. Problems with supply chain management impact patient safety, care efficiency, and revenue.
The survey highlights that 85 percent of nurses complained of long supply documentation times. Another 86 percent said they had to leave procedures to get needed items. According to 61 percent of these nurses, this raised patient safety risks.
Overall, 85 percent of participating nurses wanted more automated supply tools. Do you know how a hospital Kanban system can improve inventory processes? Keep reading to learn about this inventory management tool which has transformed supply chains in many industries, the world over.
Table of contents
- Healthcare Industry Approaches to Optimizing Supply Inventory
- What Is the Kanban System?
- Benefits of Using Kanban
- Reduced Labor Costs
- Fewer “Re-Supply” Orders
- Decrease Dangerous Lack of Supplies
- Decrease Expired Supplies
- Optimizes Supply Inventory improvement
- Implementing Your Hospital Kanban Inventory System
- Are You Ready to Streamline Your Inventory System?
Healthcare Industry Approaches to Optimizing Supply Inventory
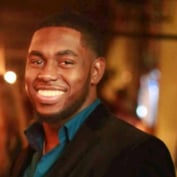
Program Manager
We asked one of our Kanban experts, Andre Kerr, Program Manager here at BlueBin, to provide some insight for medical institutions looking at Kanban to streamline their supply chain processes. Andre's been with BlueBin for over four years and has garnered a vast amount of experience and insight working alongside several major hospitals and Academic Medical Centers, supply chain managers, clinicians, and other key players who work in the supply chain processes for healthcare.
"The pandemic has certainly brought forth several challenges in supply chain. It has forced team members to take different approaches in getting supplies to support the end users’ needs. Increase in safety stock, items on allocation, and reuse of certain products are just a couple solutions," Kerr began.
Finding the optimal and most cost-efficient hospital inventory system may seem difficult. This involves finding solutions to several challenges.
Find the Right Inventory Balance
It may seem at first that ordering (and storing) extra inventory is safer and less stressful. The rationale is to always be ready to meet patient needs. But, this leads to other problems.
Excess stock means you have more of your “money” sitting on shelves. If not consumed when needed, many items begin to deteriorate or pass expiration dates. This results in regulatory issues of controlling expiring products and potentially wasting significant money.
Large inventories also take up more space and increase expenditures. You'll pay more for the physical area, utilities, temperature control, and maintenance.
Likewise, ongoing problems with supply shortages aren’t acceptable. It may cause cancellation of procedures and, thus, lost revenue. Staff frustration rises as well as patient and employee health risks.
Develop Accurate Demand Forecasting
Demand forecasting examines previous and current supply use patterns to estimate future needs. Easy to use data and visibility shows you which items have higher consumption and need higher stock levels. You’re also able to find products that are seldom used and often expire.
Inventory management solutions rely on statistical algorithms to calculate future demands. Your facility can tailor its inventory needs without sacrificing order fulfillment.
Effectively Manage Lead Times
Working with vendors to reduce wait times for delivery is key. Lack of confidence in when you’ll receive your supplies often leads to overstocking. Today, inventory management platforms help automate stock ordering and avoid this problem.
The software keeps the vendor information making it easy to automate ordering. When it detects stock levels below the set threshold, it initiates the item request.
What Is the Kanban System?
The Kanban system was first used by Toyota Production System (TPS) to keep Just-in-Time supply inventories. Kanban is simply a Japanese word that means signal. Thus, the system uses visual cues to prompt actions to streamline process flow.
Healthcare’s information technology (IT) industry adopted the Kanban system. The tools in this platform work together to track and manage the inventory.
Kanban supply bins have asset tags to keep track of the number and location of items. The system is easy to learn and use.
Benefits of Using Kanban
Kanban helps you achieve the best hospital inventory reduction and inventory balance based on accurate daily consumption. It develops prescriptive and performance analyses to guide process improvement. This tool offers the following benefits.
Reduced Labor Costs
Facilities that don’t have a supply inventory system must assign workers to this task. This means you pay for the hours it takes to manually count the number of each item.
After compiling the inventory, the staff member initiates the order process. It takes valuable time to contact vendors, secure purchase orders, and place the order.
Kanban removes the need for inventory counting. As supplies get used, they're automatically replenished. This provides huge savings in labor costs. Do more with less.
Fewer “Re-Supply” Orders
Since healthcare is ongoing and dynamic, counts may change before the employee finishes the inventory. The Kanban system learns the estimated number of items you use per day. It keeps established supply thresholds to reduce the time spent getting more supplies.
Decrease Dangerous Lack of Supplies
If you run out of supplies, it can impact healthcare delivery, patient care, and even risk lives. Kanban uses a two-bin or card visual system to reduce and/or virtually eliminate stock-outs.
The clinical staff simply pulls supplies from one bin until it’s empty. The empty bin is removed and is replaced with the second, full bin. A replenishment order is then automatically placed ensuring rotating stock and FIFO.
Decrease Expired Supplies
Kanban’s shelving system places the first items put in the bin at the front. This means they're used before older products. This lowers the risk of supplies getting pushed aside and left on the shelf until they expire.
Optimizes Supply Inventory Improvement
A thoughtfully built Kanban system is great but should be optimized by layering on reporting and/or machine learning tools to collect data about your inventory patterns. Real-time data provides reports to help you adjust your threshold quantities at any time. This allows the system to flex up and down as your needs change, such as during flu season.
Kerr goes on to add, "The complete system provides several different metrics which are used daily to assist supply chain managers in driving huddles, adjusting PARs, adding or removing items, item utilization, fill rate, and much more. BlueBin's BlueQ Analytics dashboard has proven to have been a great resource during the pandemic."
Implementing Your Hospital Kanban Inventory System
Begin by setting your desired stock levels for all items. Consider the frequency and volume of use. Identify items with shorter expiration dates and think about keeping fewer on hand.
"Implementing any new system during this pandemic can be a challenge. BlueBin uses data to help analyze how supplies are moving and identify the need in each area of the hospitals. The pandemic has changed supply utilization significantly. Traditionally, low-use items have now become items that were hard to keep on the shelves, and high-use items… well, they are difficult to keep up with. The Kanban system has helped by using that data to adjust for the needs of each product. Not only adjusting but also allowing for there to be products available in the second bin. I had a clinician approach me to say she doesn’t know what she would do without the BlueBin system because it has been a challenge getting supplies, along with only getting deliveries twice a week or not at all," Kerr added.
This helps the healthcare facility structure its Kanban systems to meet their needs. The following describes two popular set-ups for this system.
Barcode Reader System
With this method, each bin has a barcode. When all the items are taken from a bin, it is placed on the top rack of the storage rack. A full bin is pulled forward in its place.
The materials manager then scans the empty bins using a barcode reader. This quickly collects the data showing what supplies need restocking.
Barcode and QR code scanning solutions are very reliable, and contrary to common belief, efficient and nearly error-proof when standard work is applied. BlueBin implements Kanban in large health systems, academic medical centers, and children’s hospitals of all sizes.
Radio Frequency Identification (RFID) System
RFID describes the use of radio waves to identify tagged objects. Kanban systems have the ability to use RFID digital restock tagging. When the last item is removed from a bin, the worker pushes the restocking tag button.
The second bin is then used while the process for restocking the first one takes place. An automatic message notifies the materials manager that an item needs restocking. It also tells them the quantity and location of the product.
RFID was the flavor of the month a few years ago, and it does have a place in certain areas of the hospital. But this technology should be thoughtfully utilized. The benefits do not necessarily translate hospital-wide when true transformational supply chain management is what the health system is looking to achieve.
Are You Ready to Streamline Your Inventory System?
The healthcare industry has faced many challenges during the COVID-19 pandemic. One of the biggest areas impacted has been the supply chain. BlueBin offers supply chain solutions and Kanban analytics software to revolutionize inventory systems.
Our goal is to make dramatic improvements in healthcare. We strive to accomplish this by adding value to supply chain processes. This will ensure that medical providers have the supplies they need when they need them.
Contact us today to start optimizing your supply management system.