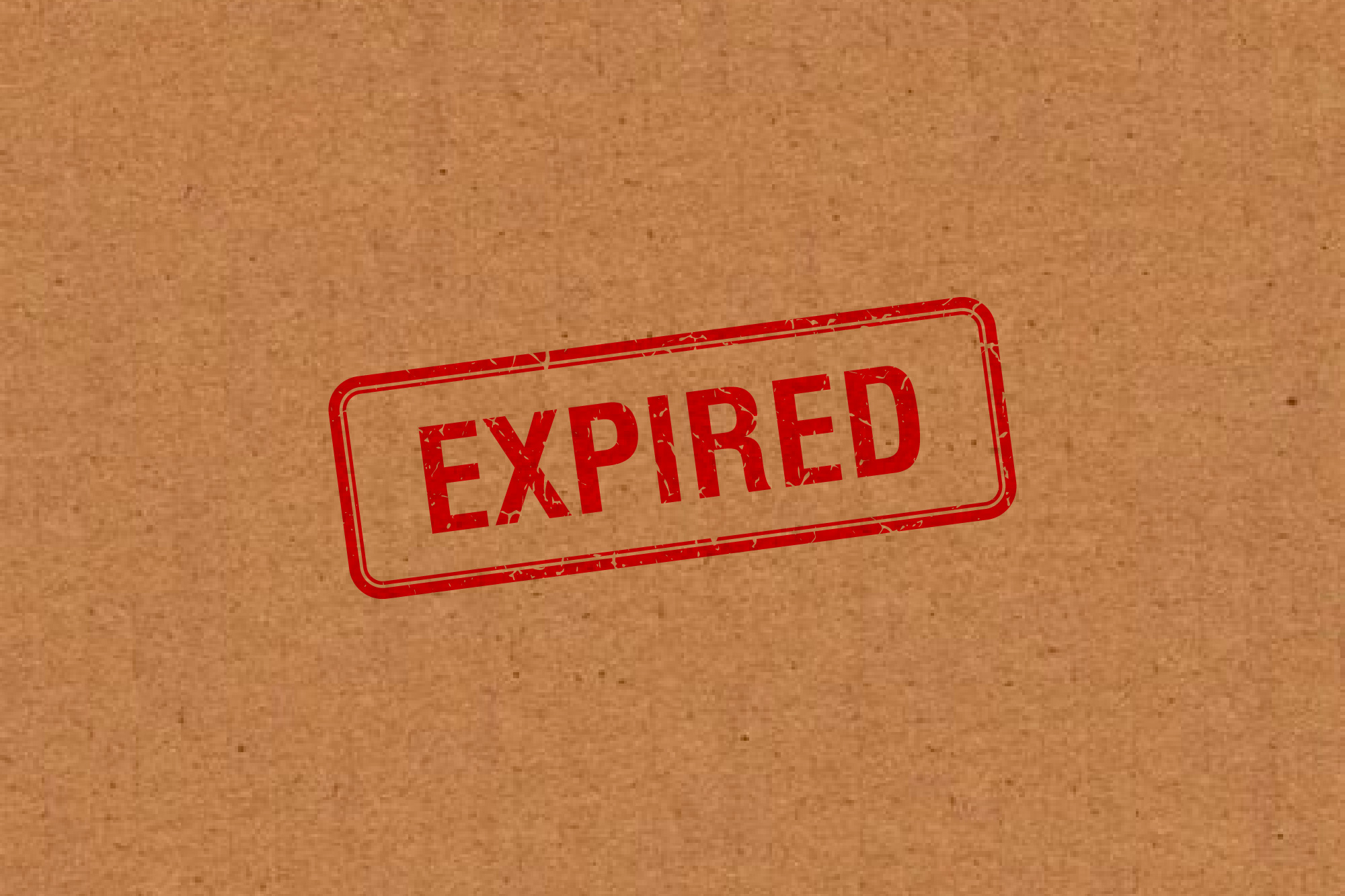
At a typical company, 20-30% of all inventory is obsolete and wasted. Obsolete inventory has posed a challenge since the development of the supply chain.
For healthcare providers and their suppliers, obsolete inventory expenses pose additional problems. Costs get pushed back onto the patient or insurance providers, making healthcare less affordable for all.
In a case study published in the Journal of Neurosurgery, a single neurosurgery department wasted $2.9 million per year on obsolete surgical supplies. The supplies were purchased, never used, and then disposed of.
In this guide, learn to tackle the problem of obsolete inventory. Read on to discover exactly what challenges healthcare organizations face and how to effectively deal with obsolete inventory risks.
What is Obsolete Inventory in Healthcare?
Obsolete inventory is excess, unusable inventory. This term describes any product that can't be used or sold due to lack of demand. It also includes items that expire before you can use them.
In healthcare, demand typically comes from physicians and staff rather than patients and data. Physician preferences can create an additional hurdle when you aim to mitigate the risk of inventory obsolescence.
Managing Obsolete Inventory: Key Challenges
Managers in every industry must contend with handling and mitigating the risk of obsolete inventory.
However, managers throughout a hospital supply chain face additional challenges. To effectively deal with obsolete inventory, managers must overcome:
- Limited or inaccurate data
- Shifting demands
- Issues stemming from "links" in the supply chain you depend on
- High cost of supplies and storage
- Insurance fraud risk
Here are some of the factors that shape these challenges.
Limited or Inaccurate Data
Limited or inaccurate data makes it challenging to order the correct amount of supplies you need when you need them. Guesswork can result in stockouts of urgently necessary supplies.
Moreover, healthcare managers may overstock on supplies that end up obsolete simply because they're trying to avoid the other extreme. Factors that limit access to accurate data include:
- Supply tracking issues (poor or no tracking technology)
- Human error in manual documentation of supply usage
- Poor supply visibility
- Outdated management software
- Software that doesn't scale effectively
Shifting Demands From Healthcare Teams, Patients
All industries deal with shifting consumer demands. However, in healthcare, patient and staff needs can be excessively unpredictable.
In 2020, the Covid-19 pandemic caused an unpredictable surge in demand for PPE.
According to an October 2021 WHO report, between 80,000 and 180,000 healthcare workers died during the global pandemic. A lack of access to PPE exacerbated risks and contributed to worker deaths.
Now, in 2022, workers and their family members have won lawsuits filed in Spain, Florida, and collectively against the United States federal government over PPE shortages.
As new diseases become crises, demands for specific medical equipment and devices change abruptly. Meaning, that the healthcare industry needs real-time data on demands more urgently than any other market.
Supply Chain Issues, Delays
For years, just-in-time ordering was the norm to save on expenses and mitigate these issues. Nevertheless, that was short-sighted.
Yet, even when hospitals attempt to order with time to spare, supply chain issues can cause unexpected delays that contribute to inventory obsolescence. Factors that cause delays include:
- Poor warehouse space management
- Supply chain complexity
- Poor communication tools, software
- Order management challenges -last-minute orders, no resiliency
- Sourcing challenges (shutdowns due to staff shortages, outbreaks)
Healthcare Supplies, Storage Costs
Obsolete inventory is costly on multiple fronts.
The supplies themselves can sometimes be expensive. So, is storing them: medical products sometimes require specialized storage, like cold storage.
This leads to unnecessary stock taking up valuable, limited space. This contributes to shortages of other, in-demand inventory.
Insurance Fraud Risk
In certain circumstances, systems automatically bill insurance companies for products that sit on shelves for more than 14 days.
If an insurance company is billed for a product prescribed to a patient, but the patient never receives (or picks up) that product, that can sometimes constitute insurance fraud.
Thus, poor management of obsolete inventory is a risk factor for inadvertent insurance fraud.
How to Manage Obsolete Inventory: Overview
Managing obsolete inventory is a three-step process.
First, identify obsolete inventory your organization is currently storing and assess to what degree your organization risks future inventory obsolescence.
Next, unload obsolete inventory properly. Aim to recoup financial losses to the most efficient extent possible.
Finally, mitigate the risk of inventory obsolescence moving forward. Implement systems, protocols, and technologies that prevent obsolete inventory.
1. Identify Current Obsolete Inventory, Future Obsolescence Risk
Inventory analysis makes your supplies both visible and quantifiable. Analytics tools can give you a clear picture of your organization's inventory strategy and the extent to which you risk losses from obsolete inventory.
This lets you determine trends and specifics to make more informed decisions in the future.
Calculate Inventory Turnover, Conduct Analysis
To calculate your inventory turnover ratio, first look at the total number of units used in a given period. Then, divide that by the average unit inventory for the same period.
Once you calculate inventory turnover, you can use that to run an inventory analysis, allowing you to track your supply chain's performance.
Determine Time of Inventory on Hand (Per Supply Type)
Inventory on hand is a key metric that gives you granular data that is relevant to each SKU.
To calculate this, multiply the cost of total units by 365. Then, divide the average inventory by the product of your first calculation.
2. Unload Obsolete Inventory Properly
As a healthcare organization, you must meet state and federal regulations regarding inventory disposal to avoid penalties.
Fortunately, it is possible to unload obsolete inventory safely. Some unload options offer opportunities to recoup losses.
Resell Obsolete Inventory in the Secondary Market
One way of recouping losses legally is to sell surplus, quality medical equipment in secondary markets. Companies can go direct to secondary marketplaces, or there are full-service companies that provide a managed service. Those managed services will sell and exchange surplus equipment and supplies; one example of this is Belmero, Inc., with their Supplier Return Managed Service.
If getting obsolete inventory out quickly is more important than recouping losses to the greatest extent possible, you may consider a liquidation service.
Specialized liquidation services purchase and remove surplus inventory at extremely low rates.
Discard Expired, Recalled, Poor-Quality Supplies
Legally, you cannot resell most expired medical supplies. These products must be disposed of safely. Consult FDA guidelines on correctly disposing of specific items (like needles and sharps).
Donate Obsolete, Functional Supplies and Equipment
Certain non-profit organizations facilitate donations of medical equipment and supplies. These organizations may de-install or pick up equipment from the hospital site. One respected non-profit is Partners in World Health.
Organizations typically give donated medical supplies to hospitals in low-income countries.
Write-Off Obsolete Inventory Per GAAP
GAAP (Generally Accepted Accounting Principles) allow healthcare organizations to write off some inventory. The write-off notes the item will not provide the organization with future economic value.
Not all obsolete inventory can be written off. For more information, see Understanding Inventory Write-Off.
3. Mitigate Risk of Inventory Obsolescence
After dealing with the current obsolete inventory, take further steps to prevent it. Inventory obsolescence is much less likely in an organization that puts preventative strategies and systems into place.
Here's what these systems look like in practice.
Implement Effective Inventory Tracking, Management Systems
Implement a system that enables effective and efficient inventory tracking and management. A quality system is:
- Visible
- Automated
- Evidence-based
For example, you may start a Kanban System. This system is simple, yet it makes on-premises inventory highly visible. This, in turn, makes tracking inventory easier.
Inventory tracking can be automated with a scanning system. This prevents human errors due to manual data entry, while the automated item tracking technology may use RFID tags and IMS software to prevent these human errors.
An evidence-based system integrates real-time data analytics into your process. It describes, predicts, and prescribes the next steps, given the current state of your inventory.
Source Strategically
Obsolete stock can happen when over-ordering. Managers sometimes over-order inadvertently to build up supply reserves. This is a defense against out-of-stocks and delays at the manufacturer or distribution level but can harm the company.
A better strategy is to source from multiple vendors, then determine the ideal reorder point for each supply. Industries could make this sourcing strategy more cost-effective while considering horizontal collaboration with other healthcare organizations.
A strategic sourcing strategy can be part of a broader enterprise resource plan (ERP). To implement it well, obtain the necessary data and determine accurate lead times.
Next, automate. Let the system place recurring orders of high-frequency supplies. This saves you time and allows you to invest in further analysis of low-frequency inventory to prevent obsolescence.
Integrate Product Quality Evaluation Into Workflow
Product quality evaluation must be routine to keep up. Build it into your everyday workflow. That way, if a supplier's products are of poor quality, you'll discover that sooner rather than later.
Supply Chain Solutions for Medical Inventory Management
Effective inventory management can mitigate the risk of obsolete inventory drastically. At BlueBin, we offer unique inventory management solutions at all levels of the supply chain.
Want to learn how BlueBin solutions can elevate your inventory management? Contact us. One of our experts will get in touch quickly.