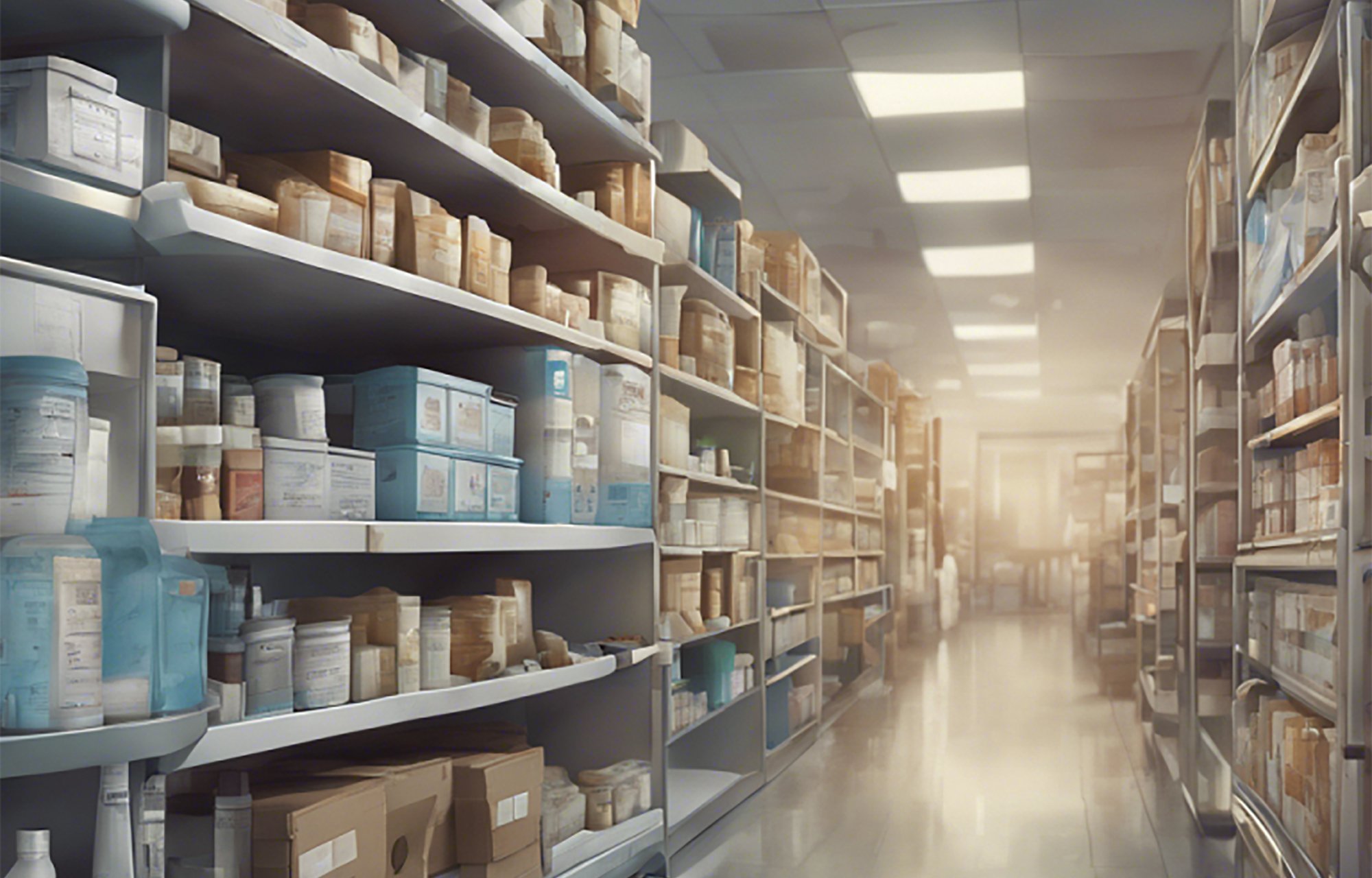
Did you know the global supply chain industry is expected to grow 11.2% from 2020 to 2027? No business can function without a functional supply chain. The problem is that shipments face many risks and disruptions that jeopardize supply chain efficiency. They may get lost, damaged, shipped to the wrong location, and so on. This makes your inventory holding costs much more expensive, and this is where a 2-bin Kanban system can help.
This system makes healthcare inventory management easier than ever before. What is so unique about this system, and what should you expect? Keep reading and learn more about this unique system below.
The Growing Challenge of Inventory Holding Costs in Healthcare
The mounting challenge of inventory holding costs in healthcare facilities causes a significant burden. The relentless drive to decrease financial outlay, improve operational effectiveness, and maintain quality patient care necessitates innovative solutions - one prominent approach is using a 2-bin Kanban system. The American Hospital Association estimates that healthcare providers spend $25.7 billion more per year on supply chain operations than necessary. That's a staggering figure, requiring hospitals to find ways to refine their inventory management and reduce these unnecessary expenses.
Inventory holding costs, sometimes called 'carrying costs,' represent the sum of costs associated with keeping unsold inventory on hand. It includes
- warehousing
- depreciation
- obsolescence
- insurance
- taxes
- opportunity costs
These costs are estimated to be approximately 25% to 30% of a hospital's total inventory value annually. Hospitals that stock excessive equipment and supplies unwittingly contribute to their fiscal strain by upholding these high carrying costs.
Whether expressed in financial terms or as a percentage of inventory value, these carrying costs can be detrimental to hospitals, particularly those with budget constraints. Strategically employing a 2-bin Kanban system in the supply chain can significantly mitigate these costs, leading to improved financial solvency and better patient care.
What Are the Current Inventory Holding Costs in Hospitals?
Inventory holding costs in hospitals and healthcare facilities refer to the expenses associated with storing and managing inventory items necessary for patient care and facility operations. These costs can include various components such as storage space, labor, insurance, and obsolescence. It is important to note that inventory holding costs can vary depending on the size and complexity of the healthcare facility and the types of items being stored.
Inventory holding costs can be significant in healthcare settings due to several factors. Healthcare facilities:
- Often need to stock a wide range of items to meet the diverse needs of patients and staff. This can include medical supplies, pharmaceuticals, equipment, and other consumables.
- Typically operate on a 24/7 basis, requiring a constant supply of inventory items to ensure uninterrupted patient care.
- Must adhere to strict regulations and quality standards, which may require storing certain items for extended periods.
All these factors contribute to the overall inventory holding costs in hospitals and healthcare facilities.
How 2-Bin Kanban Systems Work in Healthcare
Implementing the 2-bin Kanban system in healthcare requires careful planning and coordination. It involves setting appropriate reorder points and quantities, training staff on the system's principles and procedures, and establishing clear communication channels for replenishment. Regular monitoring and adjustment of inventory levels are also necessary to ensure the system's effectiveness and continuous improvement.
Understanding the 2-bin Kanban System
The 2-bin Kanban system is a lean inventory management technique that helps hospitals and healthcare facilities reduce inventory holding costs. It is based on the principles of just-in-time (JIT) inventory management, which aims to minimize waste and improve efficiency in the supply chain. The system involves using two bins or containers for each item in the inventory, with one bin being actively used while the other serves as a backup or replenishment bin.
A Kanban system utilizes visual cues to optimize replenishment procedures. Since humans are very visually driven creatures, having visual stimuli to guide us makes tasks much easier. Kanban systems are a very simple example of a visual replenishment operation. It uses visual signals to get things done, and specific visual signals may cause certain supplies to move to a different location.
These visual signals make it easier to keep track of various supplies and materials. You can track where the supplies go, what stage of the production process they're in, and so on. This reduces the risk of items getting lost at any point during the production or shipping process.
Reducing Inventory Holding Costs
Let’s delve further and understand how exactly this system reduces inventory holding costs. Hospitals and healthcare facilities typically store more items than required due to uncertainties regarding usage and delivery time. However, this approach invariably leads to an inflated holding cost. A 2-bin Kanban system addresses this issue in two main ways:
- Optimized Inventory Levels: By using a system that triggers restocking at the right time, hospitals can maintain a lean inventory, i.e., a balance between the necessary surplus and the requirement. Minimizing "excess" inventory cuts down the holding cost significantly.
- Elimination of Waste: Waste generated due to expiration or product damage is a typical scenario in many healthcare facilities. The Kanban system promotes usage on a “first in, first out” basis, thereby reducing the possibility of products reaching their expiry before use.
These two actions, when combined, lead to an overall reduction of the capital tied up in inventory, translating into lower holding costs.
Added Benefits of 2-Bin Kanban Systems
Another benefit is increased efficiency in the supply chain. With a 2-bin Kanban system, healthcare facilities can streamline their procurement processes. The system provides a visual signal when supplies in one bin are depleted, triggering the replenishment process. This eliminates manual inventory checks and reduces the time and effort spent on procurement activities. As a result, healthcare providers can focus more on patient care and allocate resources more effectively.
Additionally, implementing a 2-bin Kanban system can enhance patient safety. healthcare facilities can minimize the risk of treatment delays or errors due to stockouts by ensuring that necessary supplies are always available. This can have a direct positive impact on patient outcomes and satisfaction. Moreover, the system promotes standardization and consistency in inventory management practices, reducing the likelihood of medication or equipment shortages that could compromise patient care.
Making the job more enjoyable and keeping workers motivated, a Kanban system potentially provides plenty of growth opportunities for workers. Since this system does most of the heavy lifting, they can use their time to focus on other important tasks or endeavors.
The Knock-on Effects
In the long run, this reduction in holding costs not only aids in cost reduction but also introduces a degree of efficiency and predictability in hospital operations. An optimized inventory system means that the medical staff can trust the availability of the necessary supplies when needed. This improves patient care, reduces stress among staff, and fosters a more efficient healthcare ecosystem.
With the implementation of a 2-bin Kanban system, hospitals stand to reduce their average holding costs dramatically. As the demand for healthcare facilities to be efficient and cost-effective intensifies, leaning toward solutions like these seems not only practical but necessary.
A Kanban system also creates efficiencies to curb transportation expenditures. However, the foremost objective remains fulfilling hospital demand for essential supplies when urgent needs arise. By bolstering supply chain reliability, Kanban methods help strengthen the capacity of healthcare providers to deliver timely treatment and lifesaving care to patients.
Kanban Systems Reduce Inventory Holding Costs
Healthcare environments can often be unpredictable. But Kanban systems help account for that unpredictability. These systems make it easy to think ahead and solve problems before they happen. Ensuring supplies get where needed, even when a problem arises, and helping eliminate unnecessary or outdated items, reducing waste.
The mounting challenge of inventory holding costs in healthcare settings requires a strategic solution. The 2-bin Kanban system, a lean inventory management strategy, emerges as a viable tool in this milieu. This simple yet innovative system can offer healthcare facilities and hospitals much-needed fiscal breathing room by significantly reducing inventory holding costs.
Furthermore, the knock-on effects of using this system ripple beyond just monetary savings. It can improve efficiency, elevate patient care, and increase staff satisfaction. Thus, it is incumbent on healthcare administrators and decision-makers to explore this approach, learn more about how it operates, and consider its implementation within their facilities.