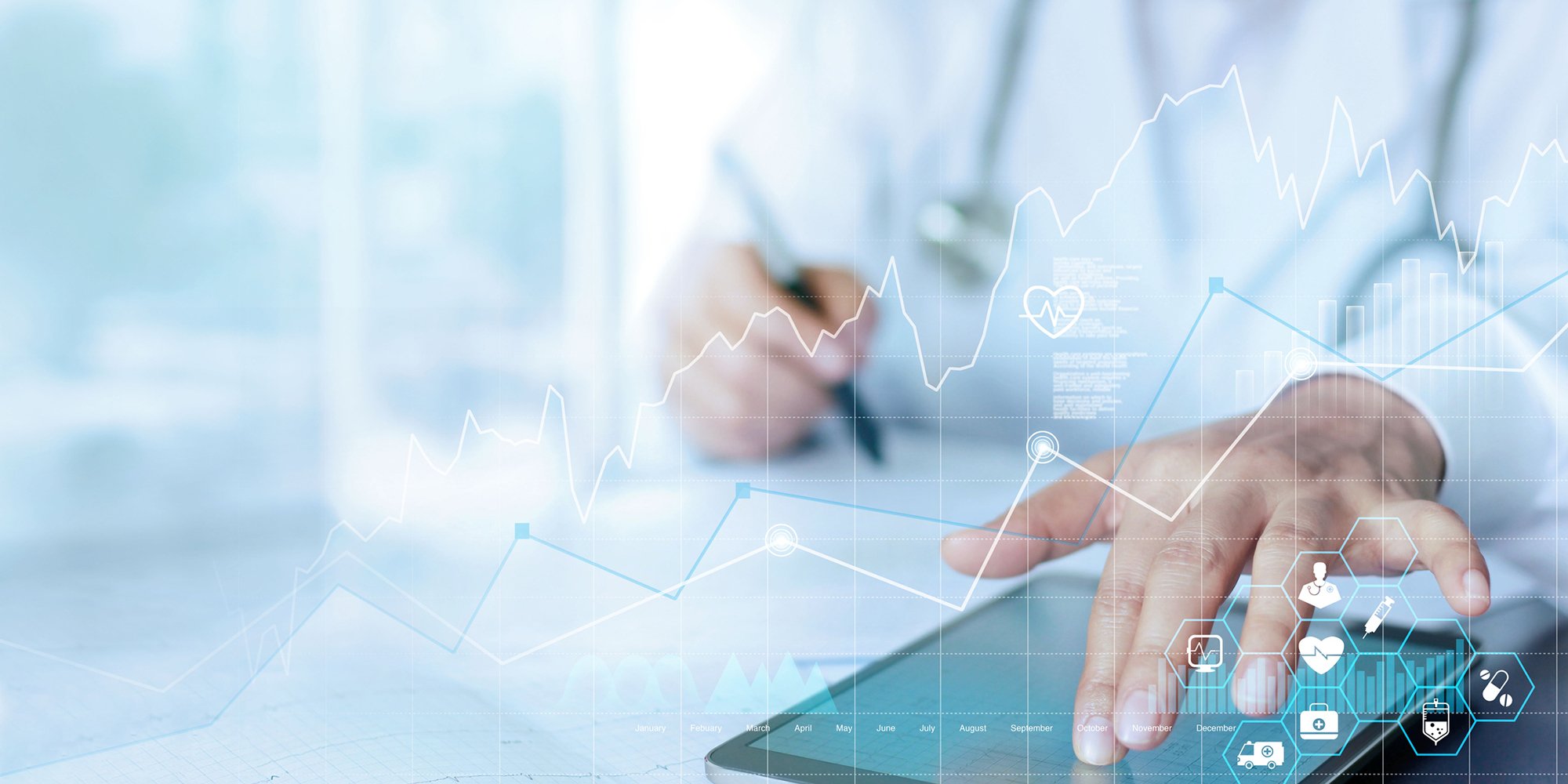
In modern healthcare, the efficiency of the supply chain directly impacts patient care quality. A well-managed supply chain ensures medical professionals have the necessary tools and resources, reducing delays and enhancing treatment outcomes. This comprehensive blog explores the importance of understanding clinical perspectives, the advantages of point-of-use systems, and the transformative power of automation and technology integration in hospital supply chains.
Understanding the Clinical Perspective
A thorough grasp of clinical needs is crucial for an effective supply chain system. Each department, whether the ER or the OR, has distinct requirements for customized solutions. Understanding and addressing these unique needs can significantly improve the supply chain’s efficiency and effectiveness.
Key steps in leveraging clinical insights:
- Partnering with clinical staff
- Data-driven analysis
- Tailored solutions
Partnering with Clinical Stakeholders
Optimizing a hospital's supply chain hinges on effective collaboration. Engaging clinical stakeholders like nurses, doctors, and department heads can gather valuable insights into their specific needs and challenges. Regular meetings, surveys, and focus groups offer a comprehensive understanding of clinical staff's daily issues. Including them in the process yields critical information and fosters a sense of ownership and commitment to the new system.
Analyzing Consumption Patterns Across Specialties
Different medical specialties have specific supply requirements. For instance, orthopedics often needs a regular influx of implants and surgical instruments, whereas the ICU relies on various consumables. Examining historical data and usage patterns helps uncover trends, seasonal changes, and anomalies. This information is vital for developing a robust replenishment system, ensuring that every department is always adequately stocked with the necessary supplies.
Tailoring Systems to Meet Departmental Needs
The insights obtained from collaborating with clinical stakeholders and analyzing data should inform the creation of tailored solutions for each department. This could mean implementing varying PAR levels, unique storage configurations, or specialized ordering procedures. Customizing the system in this way ensures it integrates smoothly into each department's workflow, enhancing efficiency and minimizing interruptions to patient care.
The Power of Point-of-Use Systems
Point-of-use (POU) systems like the Kanban method revolutionize hospital inventory management. These systems bring supplies closer to the point of care, improving efficiency and reducing waste. By leveraging technology, POU systems enable healthcare providers to easily track inventory usage, ensuring that supplies are always available when and where they are needed most.
Eliminating Guesswork in Reordering
Conventional inventory management often relies on manual counting and subjective judgments of stock levels. In contrast, point-of-use systems provide a standardized, visual approach to managing inventory. By employing two-bin systems or electronic PAR-level indicators, staff can easily see when it's time to reorder, removing the guesswork and significantly reducing the potential for human error.
Reducing Errors and Stockouts
One of the most significant benefits of POU systems is their ability to reduce stockouts and overstock situations dramatically. Maintaining optimal inventory levels ensures that critical supplies are always available when needed, enhancing patient care and safety. At the same time, these systems prevent overstocking, which ties up valuable financial resources and increases the risk of product expiration.
Freeing Up Clinical Staff to Focus on Patient Care
In numerous hospitals, clinical staff often spend considerable time managing supplies, which could otherwise be spent on patient care. Point-of-use systems automate inventory management, alleviating this burden from healthcare professionals. This enhances job satisfaction and enables staff to focus more on their core responsibility: providing care to patients.
Automation and Technology Integration
Automation and advanced technologies are elevating point-of-use systems to new heights, delivering unmatched efficiency and accuracy in supply chain management. These innovations are especially valuable in hospital environments, where precision and timely resource management are critical.
RFID Tracking for Real-Time Inventory Updates
Radio-frequency identification (RFID) technology transforms hospital inventory tracking by offering near-perfect accuracy. Attaching RFID tags to supplies and equipment eliminates the need for manual counts. RFID-enabled cabinets and shelves automatically detect when items are added or removed, updating inventory levels in real time. This innovation boosts accuracy, strengthens security, cuts labor costs, and generates valuable data on usage patterns.
AI-Driven Predictive Analytics for Smarter Ordering
Artificial Intelligence (AI) is advancing hospital supply chain management with greater sophistication. AI-driven systems analyze historical data, current usage patterns, and external factors such as seasonal trends and upcoming procedures to forecast future supply needs. These predictive capabilities help optimize order quantities, recommend optimal PAR levels, and foresee potential shortages before they arise.
Integration with Electronic Health Records for Seamless Patient Care
Integrating supply chain systems with Electronic Health Records (EHR) represents a significant leap forward in healthcare efficiency. By linking supply usage directly to patient care, hospitals can achieve a new level of precision in inventory management. For example, when a doctor orders a specific treatment in the EHR, the system can automatically check supply availability, trigger reorders if necessary, and suggest alternative products if the preferred item is out of stock.
Ensuring Consistent Use of the System
Consistency is the backbone of successful automation in hospital supply chains. To fully benefit from these systems, it's essential to ensure all users are on board and committed to correctly using the technology. This often begins with effective training programs that cater to diverse learning styles, allowing all staff members to understand the system's functionalities and advantages.
Reducing Human Error
Even the most meticulous staff can make errors when managing inventory manually. Automated systems significantly reduce these human error risks. For instance, RFID technology tracks item removal in real-time, providing accurate usage data without manual counting. Similarly, barcode scanning systems ensure products are correctly stocked in their designated locations, preventing potentially serious mix-ups in a healthcare environment.
Increasing Overall Efficiency
Automation minimizes errors and significantly enhances the speed and efficiency of the entire supply chain process. Automated systems can handle reorder requests instantly, update inventory levels in real-time, and produce reports and analytics without manual intervention. This boost in efficiency leads to time savings for staff, cost reductions for hospitals, and, ultimately, improved patient care.
Conclusion
Integrating clinical perspectives, point-of-use systems, and advanced technologies into hospital supply chains can revolutionize how healthcare facilities manage their resources. Hospitals can ensure a consistent, accurate, and efficient supply chain by understanding and addressing each department's unique needs, utilizing efficient POU systems, and embracing automation and technology. This enhances patient care, optimizes resource allocation, reduces waste, and improves overall hospital efficiency.
Innovative solutions that BlueBin offers play a crucial role in this transformation. By offering real-time data and user-friendly interfaces, BlueBin helps healthcare facilities minimize manual errors, streamline processes, and ensure the timely availability of supplies. Our supply chain management expertise and personalized support position us as partners in driving efficiency and enhancing patient care. Let us help you redefine your hospital's supply chain for a more responsive and reliable future.
Download the Whitepaper Now. Catch on early to supply chain inefficiencies that hold your hospital back. Take the first step towards a more efficient, cost-effective, patient-centered supply management system today.